Version 26 of hsbMake
Production Grouping
The new Production Group feature, designed to enhance flexibility in managing and grouping production orders and projects. This feature allows users to group batches and orders, optimizing how loads are dispatched into the factory and providing greater control over production processes.
- The new Production Grouping functionality also extends to the end of the production line, allowing users to consolidate batches from different orders into production groups. Once these groups reach the end of the line, they are automatically dispatched as a single unit. This process concludes with the generation of a dispatch note, transforming grouped batches into an organized stack, ready for shipment or further handling.
- The new Production Grouping functionality also extends to the end of the production line, allowing users to consolidate batches from different orders into production groups. Once these groups reach the end of the line, they are automatically dispatched as a single unit. This process concludes with the generation of a dispatch note, transforming grouped batches into an organized stack, ready for shipment or further handling.
Quality Checks
This addition significantly enhances our capabilities by allowing Production Management to implement and manage customizable quality checks for offsite timber production.
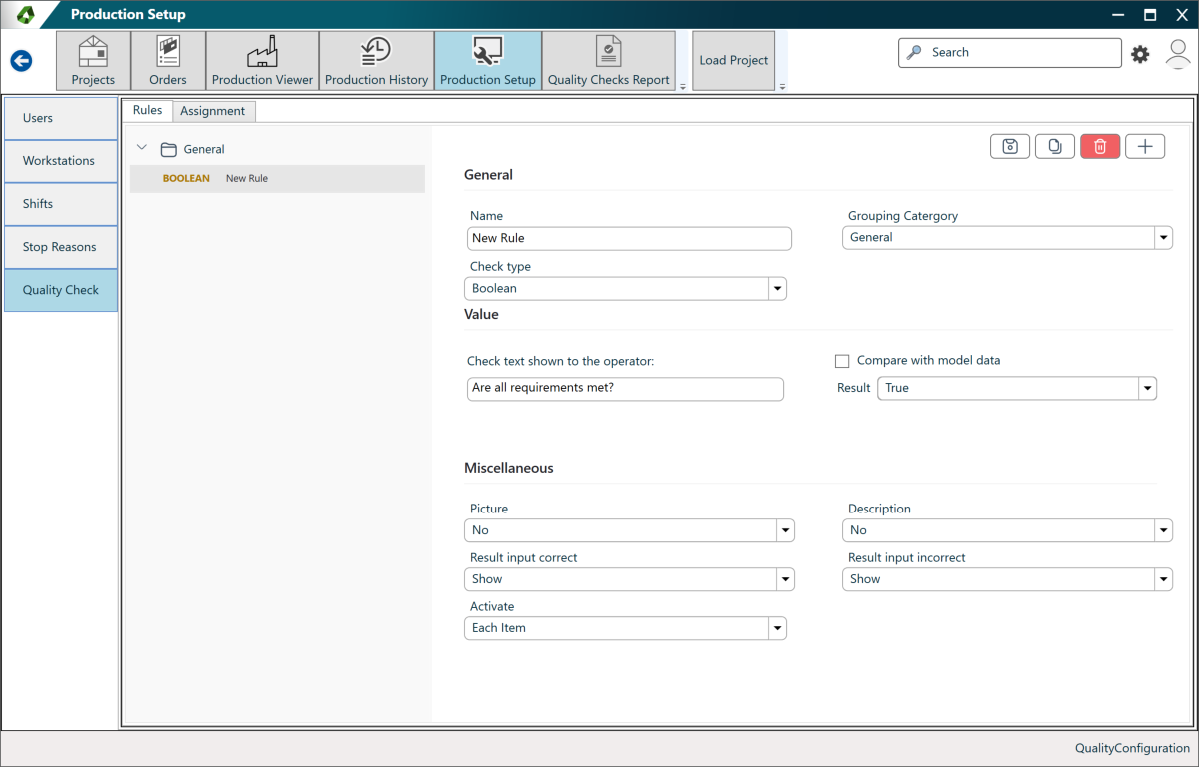
Customizable Quality Checks:
- Flexible Configuration: The Production Management team can define the specifics of each quality check. This includes the type of check, its frequency, the goal, and the subject of the check.
- Detailed Specifications: Managers can set precise requirements, such as specific measurements that need to be taken. That way, the operators can provide real data, descriptions and attach photos to ensure clarity and accuracy.
- Design Comparison: Measurements taken during production can be directly compared with the hsbcad Model data, ensuring that the final product aligns perfectly with the design. The tolerance can also be set up directly in every check.
Seamless Operator Integration:
- Automated Notifications: Operators will be notified automatically if an item in production requires a quality check. This integration means that the operator’s workflow remains uninterrupted, with checks being seamlessly integrated into their routine tasks.
- Mandatory Checks Before Booking: Quality checks must be completed before the item can be booked out, ensuring that no step is missed in maintaining high standards.
Comprehensive Record Keeping:
- Data Recording: hsbMake records every performed check, capturing all relevant information, including timestamps, photos, and any actions taken if repairs were necessary.
- Exportable Documentation: The entire record of checks, including all associated data, can be exported. This is especially valuable for external Quality Control audits or for maintaining thorough documentation of production quality.
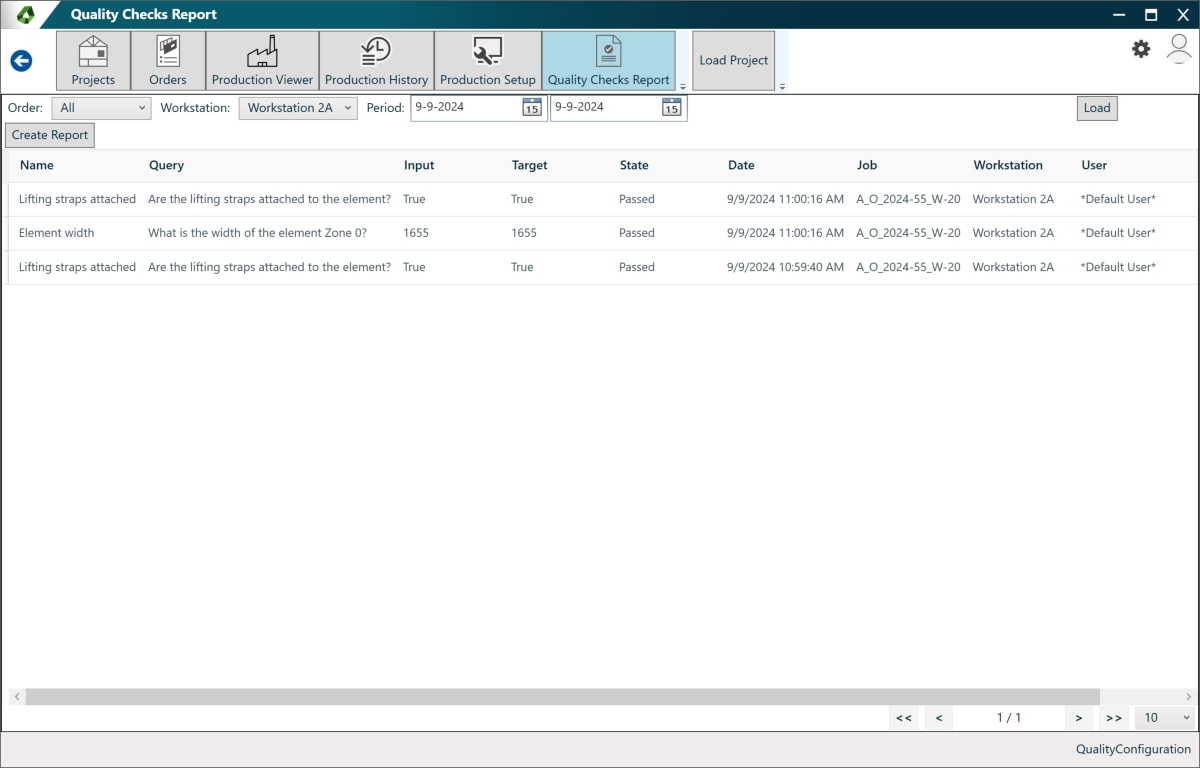
Label Printing
We are excited to introduce the new Label Printing feature, an improvement designed to streamline your workflow by automating label printing based on specific movements within the controller. This feature allows you to trigger label printing whenever a job enters or leaves a unit, providing greater efficiency and accuracy in managing your operations and removing manual dependencies or steps.
BOMLink
You can now enrich your ModelX files with supplementary data during the upload process from hsbDesign to hsbMake. This enhancement allows for setting estimations and assigning them to various types of elements or routings, providing greater flexibility and accuracy in project planning.
Besides setting these estimations manually based on for example element types, you can also use BOMlink now. The integration with BOMlink enables more advanced analysis and calculations as part of the export routine. BOMlink can be used as an analyzer, allowing complex scenarios to be examined and computed, enhancing the overall functionality and value of the export process.
Operations - Operation steps support
We are pleased to announce the introduction of Operations Support in the Module Client and Master Panel cutting, a feature that enhances the visibility and management of individual operations within the production process. This feature enables users to track and manage specific operational steps within a job, allowing for more granular control and flexibility.
- For example: Operation steps: Each model inside Module station is an operation step, now you can finish 2 of the modules for example, then someone else can book and start processing the modules. The system keeps track of the operations – the next booked job knows where to continue and which operations were already finished.
ERP integration
We have improved our ERP integration framework, making it easier and more efficient to link with various ERP systems. This enhancement introduces a standardized format for communication with ERP systems, streamlining the process of integrating and exchanging data.
Issue Manager
In addition to the improvements made to our ERP integration framework, we have introduced an Issue Manager to effectively manage and monitor communication with ERP systems.
More control in Make Office
We are enhancing user control by relocating external settings, which were previously managed on the server, into the hsbMake Office application. This change empowers users to directly modify these settings within the application, simplifying the process of making adjustments and enhancing the flexibility and efficiency of managing their projects.
Also the Export Manager, Extension Group Manager and the Validation Manager are now accessible directly through hsbMake Office, allowing users to manage exports more easily and quickly. This integration streamlines the workflow, providing quick access to export functionalities and enabling users to perform export tasks efficiently without needing to navigate through separate systems.
Versioning
Sync between versions Office and Server
We have enhanced the versioning system to ensure better synchronization between server and locally installed versions of hsbMake. This improvement helps avoid version conflicts by ensuring that users have the same version installed across platforms.
Upon starting hsbMake Office, the system checks the server for version alignment. If out of sync, users are prompted to start the support tools to resolve discrepancies (update to the version of the server).
Multiwalling based on stacks
We have enhanced the production line process to support the efficient stacking of panels and multiwalls. This new feature allows factory operatives to build stacks directly from panels coming off the production line without needing to set walls aside, improving efficiency and safety.
Details:
- Direct Stacking: Every panel that exits the production line can now be immediately added to a stack, reducing the need for intermediate storage and manual handling.
- Optimized Sequencing: The production line now sequences multiwalls in a way that allows them to be added to stacks straight away, minimizing disruption and maximizing space utilization.
- Limited Open Stacks: The system takes into account the limited number of open stacks available, ensuring that multiwalls are created and stacked efficiently within the constraints of the factory space.
- Benefits: This improvement makes the stacking operation more efficient and safer, requiring less manual intervention and optimizing the use of available storage space.
Interaction with CNC Data
We are introducing a new capability that enables real-time interaction with CNC data by injecting the location where modules were built into the WUP files. This feature ensures that Weinmann machines are informed about the precise origin of materials, optimizing production processes.
Packing and picking tickets
We have introduced a new feature that allows for the generation of picking and packing tickets, streamlining the process and enhancing organization and efficiency in the factory.
Details:
- Picking Tickets: Users can now generate picking tickets that detail what needs to be picked for a specific order or batch. This feature ensures that all necessary components are gathered accurately and efficiently for production.
- Packing Tickets: Packing tickets can be generated to specify what needs to be grouped at the end of the production line and how it should be organized. This helps ensure that all products are packed correctly for dispatch, reducing errors and improving workflow.
- Benefits: The generation of picking and packing tickets improves accuracy and efficiency in the picking and packing processes, helping to minimize errors and streamline operations.
Reporting
We have introduced the ability to export workstation job logs, providing a detailed overview of which elements or items are processed at each workstation, along with precise timing data. This feature supports production operators and office staff in monitoring and analyzing workflow efficiency. Additionally, you can leverage this export using the external data visualization tools such as Tableau or Power BI to build custom reports and dashboards.
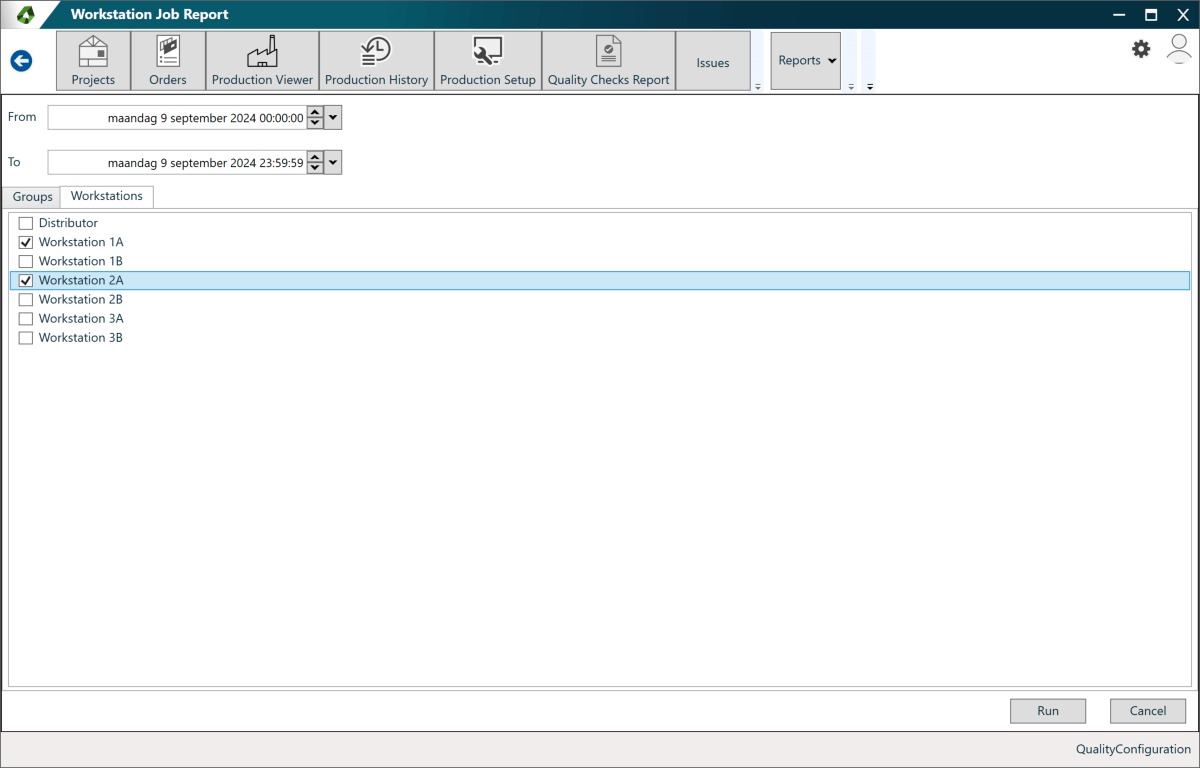